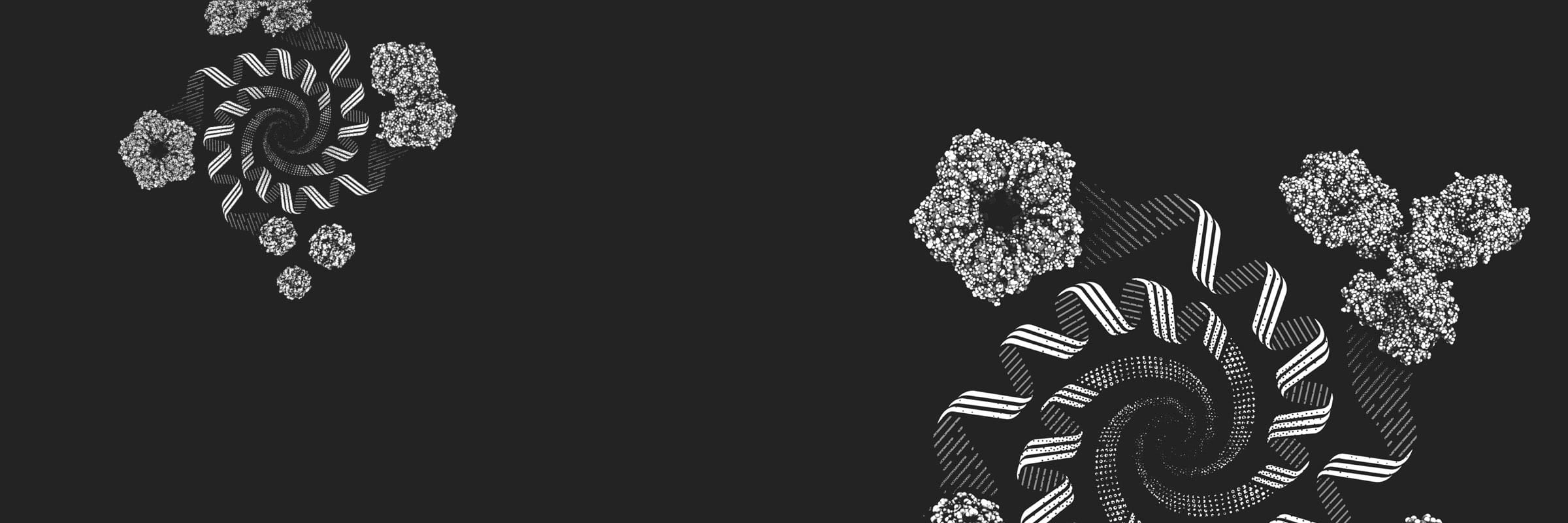
$60M PROGRAM jointly funded with CEPI
R3
We need a global network of RNA biofoundries.
In one of the greatest scientific accomplishments of our generation, mRNA technology has demonstrated the ability to change the timeline for developing and delivering a new vaccine from years to months. And the entire world was witness to that demonstration. The development of an mRNA- based vaccine for COVID-19 took just 63 days from release of the virus sequence to first dosing in humans, leading to accelerated clinical trials, and ultimately billions of doses manufactured.
The scale of this on-going achievement was made possible because RNA technology shifts the most difficult and complex parts of manufacturing— the key proteins needed for a vaccine—to the natural bioreactor that is the human body. This shift meant the mRNA vaccine could deliver the instructions for how to make the antigen, or spike protein, needed to train our immune systems rather than the antigen itself. The development of lipid nanoparticles (LNPs) ensured that instructions would arrive intact to our cells – a critical element of the mRNA vaccine delivery and effectiveness.
Such success is catalyzing increased investments in RNA-based products; however, the discovery and development of these products is still subject to the same limitations chronically afflicting biologics: difficult access to current good manufacturing practices (cGMP) material for clinical trials as well as long and large investments (4-8 years and $300 -$500 million dollars) in bespoke, manufacturing processes at dedicated facilities. This limits innovation and creates prohibitive production costs.
These limitations bear similarities with the limitations faced by the semiconductor industry at the end of the 1970s. In the twenty years following the invention of the first integrated circuit in the late 1950s, the design of semiconductor-based products was almost exclusively confined to a handful of large, vertically integrated companies that could afford the investments required by customized ISO-certified manufacturing processes. And designing a new semiconductor-based product was limited to employees within those companies.
Then, in the decade after 1978, the number of new start-ups more than tripled – tens to dozens of new semiconductor start-ups. The decoupling of design from fabrication and the parametric abstraction of fabrication processes made it possible for a greater number and diversity of people to design integrated circuits and enabled any of these designs to be fabricated at any of a multiplicity of fabrication sites at scale and seamlessly. Since then, continued process improvements, the emergence of different lines for different classes of products, and optimization of production load balancing, has led to new speed and vibrancy in the ecosystem, further fueling additional breakthroughs.
“The application of mRNA to emergency vaccine development has achieved extraordinary validation through the response to COVID-19.
We need to optimize the core technology, accelerate development and manufacturing timelines, and ensure equitable access. R3 is dedicated to achieving these ends for vaccines and beyond.”
— Richard Hatchett, CEO of CEPI
Program Director.
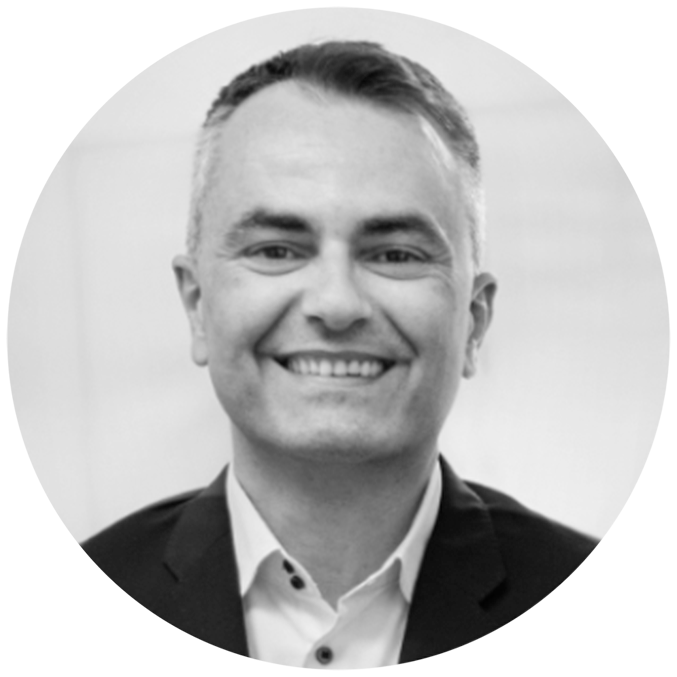
Further details.
To learn more about the program history, performer teams, and process, please visit the Program Details Page.